近年来,随着我国汽车制造业的迅猛扩张,冲压模具行业呈现出显著的增长势头,年增长率达到了20%。这一技术密集型产品在冲压生产中扮演着不可或缺的角色,其设计和制造直接影响着冲压件的质量、生产效率以及成本。在汽车产品的整个生命周期中,车身模具的开发尤为关键,其设计制造占据了整个开发周期的三分之二,是推动新车型迅速上市的关键因素。在我国,中高端模具市场大约有50%的份额被进口模具占据。
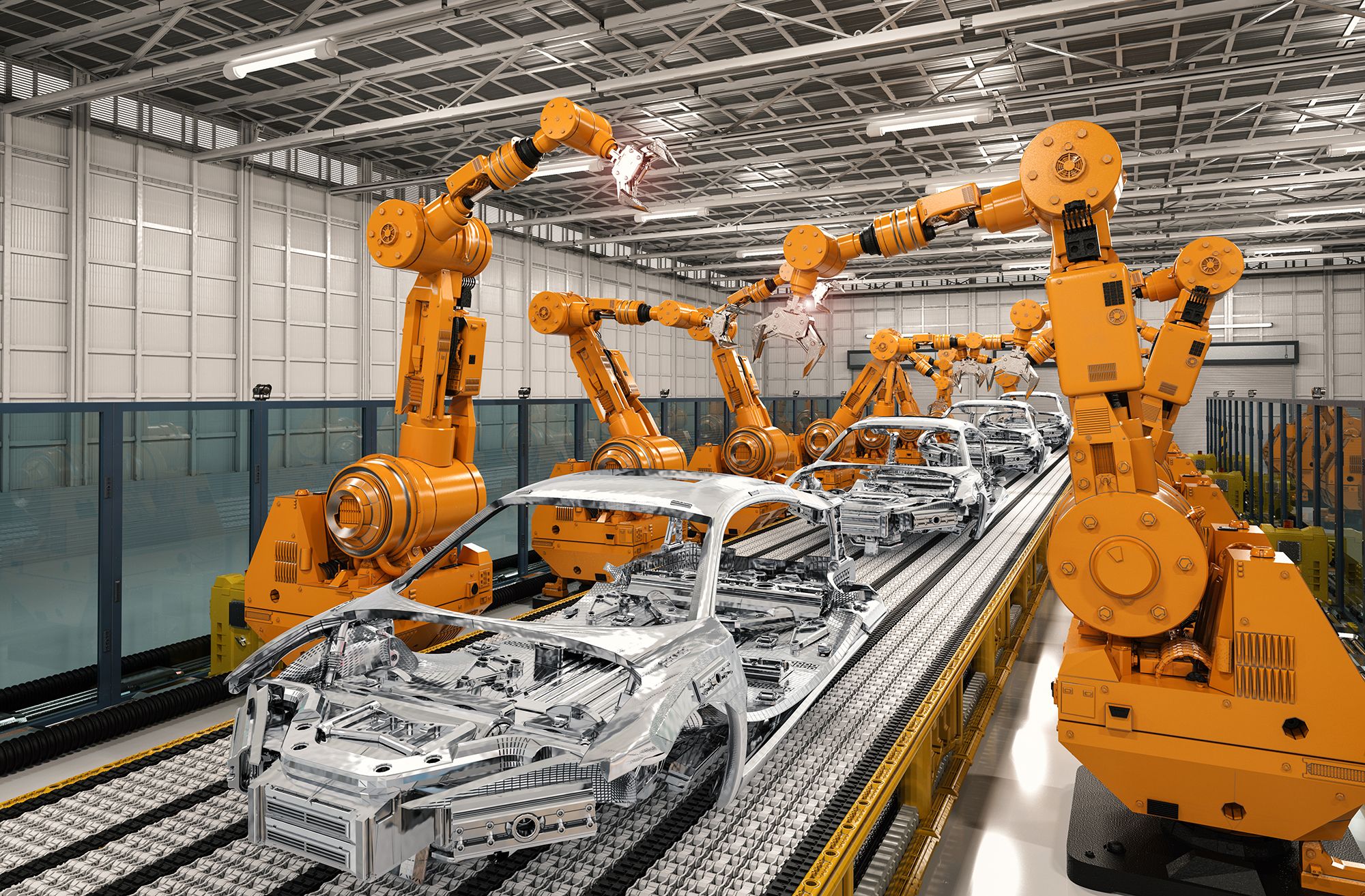
一、汽车模具类型与加工设备特点
汽车冲压模具的种类繁多,可以根据其工作性质、结构以及材料进行分类。其中,根据工艺性质,模具可以分为冲裁模、弯曲模、拉深模、成形模等;根据工序组合程度,可以分为单工序模、复合模、级进模等;根据产品的加工方法,可以分为冲剪模具、弯曲模具、抽制模具、成形模具和压缩模具等。
冲压模具分类
按工艺性质分类:
冲裁模:使材料沿封闭或敞开轮廓线分离,如落料模、冲孔模等。
弯曲模:使板料毛坯沿弯曲线弯曲变形获特定角度和形状工件。
拉深模:将板料毛坯制成开口空心件或改变空心件形状尺寸。
成形模:使毛坯或半成品按凸、凹模形状复制成形,材料仅局部塑性变形,如胀形模等。
按工序组合程度分类:
单工序模:压力机一次行程完成一道冲压工序。
复合模:压力机一次行程在同一工位完成两道或以上冲压工序。
级进模(连续模):在毛坯送进方向有两个或更多工位,压力机一次行程在不同工位逐次完成两道或以上冲压工序。
依产品加工方法分类:可分为冲剪模具、弯曲模具、抽制模具、成形模具和压缩模具。冲剪模具以剪切作用工作,弯曲模具将毛坯弯成一定角度,抽制模具将平面毛坯制成有底无缝容器,成形模具用局部变形改变毛坯形状,压缩模具利用压力使金属毛坯变形。
二、汽车模具的设计制造全面推广数字化
模具数字化技术内涵:是计算机技术或计算机辅助技术在模具设计制造中的应用,包括 CAD/CAE/CAM/DNC 技术,能提高模具生产效率、质量和企业综合水平效益。
数字化汽车模具生产技术内容:
可制造性设计(DFM):设计时考虑可制造性。
型面设计辅助技术:发展智能化型面设计。
CAE 辅助分析和仿真:预测和解决冲压成形缺陷问题。
三维模具结构设计取代二维设计。
模具制造采用 CAPP、CAM 和 CAT 技术。
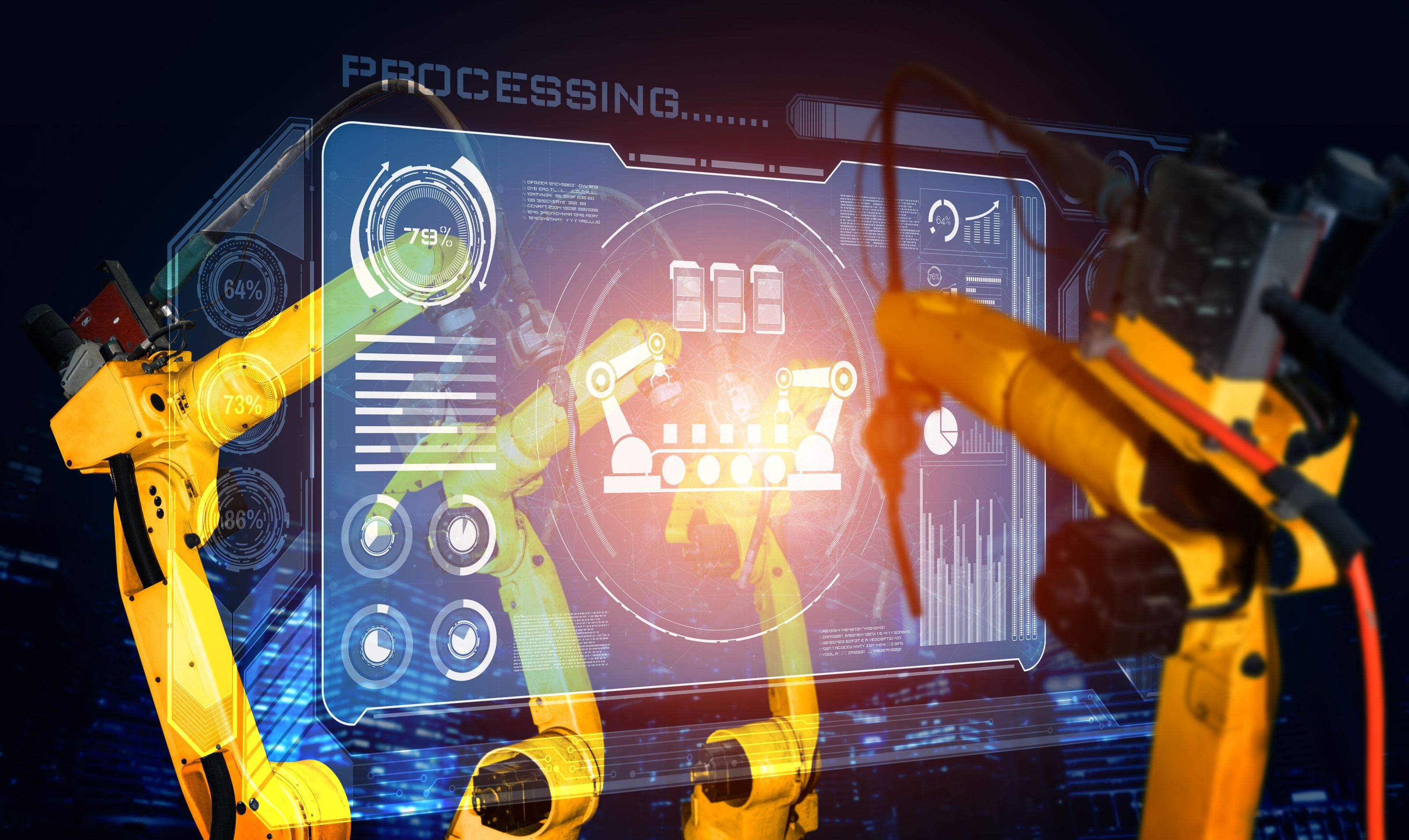
三、数字化指导下处理试模和冲压生产问题。
数字化技术发展条件与优势:微机软件发展使 CAD/CAM/CAE 技术普及条件成熟,计算机和网络促进其跨地区等推广,高速扫描机和模具扫描系统可缩短模具研制周期,实现 “逆向工程”。汽车冲压模具设计除 CAD 软件还应用有限元模拟软件,如 AutoForm 可模拟薄板成形等过程。数字化与智能化是国内模具行业发展新方向。
模具型心及电极加工模块化
模具中心组成与运行:由电火花成形加工机床、CNC 高速加工中心、料库和机器人组成,任务管理系统协调加工,料库有可识别芯片的工件托盘和电极夹头,机器人和机床可精确识别工件和电极,可连续 24 小时运行,工件一次装夹完成 CNC 加工和 EDM 放电加工,提高加工质量、速度和产量,缩短生产周期。
加工工艺集成优势:将电火花成形加工和高速铣削集成,发挥各自工艺优势,提高设备生产效率、缩短制造时间和模具生产周期、提高加工精度和机床使用率、降低成本。
自动化集成解决方案与 EDM 发展趋势:自动化集成解决方案应由同时生产电火花加工机床和高速铣床的厂家供应,便于维护检修。EDM 在复杂型面等加工有优势,今后将提高其效率、自动化程度、表面完整性,向绿色 EDM 新技术发展。
四、汽车模具一次到位的精细化加工
精细化加工目的与管理方向:减少钳工研修,一次加工到位,降低反复加工等对钳工技艺的依赖,实现 “直接装配法”。
实现精细化加工途径:从模具设计、数控编程和数控加工入手,利用 CAE 技术精细化设计模具,如拉延模针对进料量设计拉延筋等。需要高刚度、高精度、高转速的高速精密数控铣床和高速刀具,重视数控编程技术,包括等高线加工等方法。
精细化制造保障:靠技术和管理保障,如丰田公司在模具型面设计中积累经验,初次试模时规范钳工操作,记录试模缺陷。高速切削加工技术提高模具型面加工精度,国外一些企业通过多种技术综合应用提高模具设计制造可靠性。
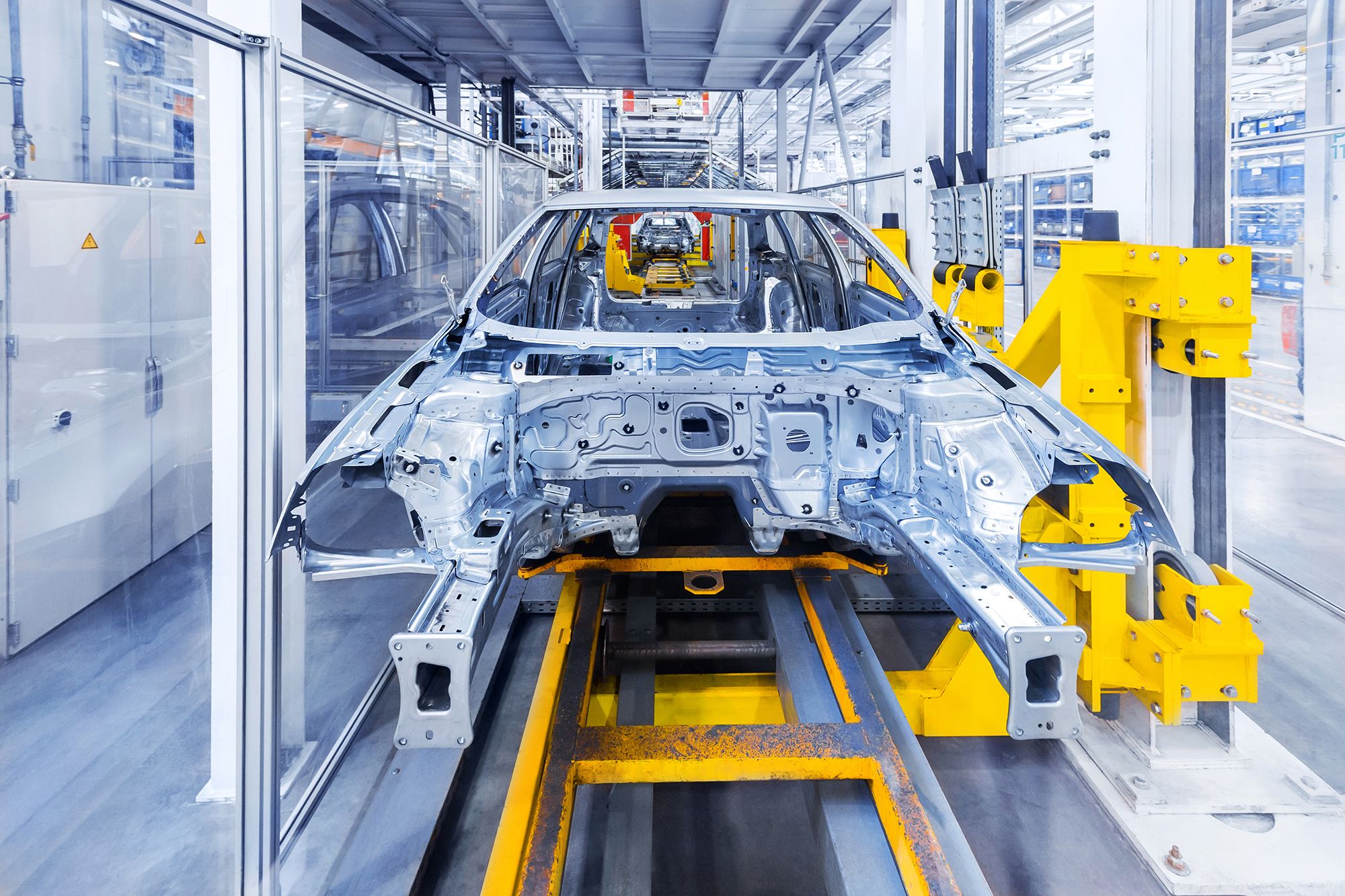
五、汽车模具快速原形制造技术
快速制模(RPM)技术原理与优势:依据快速成型制作的样模,采用拷贝方式快速制造模具主要工作零件,制造周期短(为传统数控切削方法的 1/5 - 1/10),成本低(为其 1/3 - 1/5)。是综合多种技术的先进成形方法,可直接或间接用于模具制造,具有技术先进、成本低、周期短、精度适中等优点,适用于新产品开发试制等多种情况,有良好发展趋势。
总之,我国汽车工业发展带动汽车模具行业发展,模具产业要满足用户高精度、短交货期、低成本要求,需提高生产能力,应用先进制造技术,调整行业内部结构,提高技术水平,实现模具企业向技术集成化等方向发展,实现跨越式发展。